Point-of-care printing, soil sensors and advanced manufacturing: K-State drives next-gen tech
Carl R. Ice College of Engineering faculty are developing teaching, research and engagement opportunities for next-generation industrial and mechanical technologies.
a next-generation land-grant university. Everything K-State does as an institution falls into one of these three buckets.
eaching, research and service. These are the three pillars of Kansas State University’s mission asYear after year, faculty in the Carl R. Ice College of Engineering secure grant-funded projects that deliver on all three of these fronts, while maintaining their focus on developing new technologies and finding new efficiencies that continue to improve society and solve global challenges.
What follows are three examples of this idea in action: the creation of a new course on point-of-care additive manufacturing, the design and production of nanoscale soil sensors for precision agriculture, and the development of engagement and innovation with small businesses and entrepreneurs across Kansas and beyond.
Doctoral students Asif Raihan, Isaac Obembe and junior Xania Cobian, all in industrial and manufacturing systems engineering, work with associate professor Meng Zhang, second from right, in his research lab.
Finding a new passion through education
K-State’s top priority has always been student success.
But students can’t be successful without access to state-of-the-art technology and relevant coursework that prepares them to work in cutting-edge, growing fields.
Meng Zhang, associate professor of industrial and manufacturing systems engineering, took that idea and applied for external funding to create a new engineering course focused on the emerging health care field of point-of-care additive manufacturing, which uses a 3D model to create physical objects based on medical imaging data at the place of patient care.
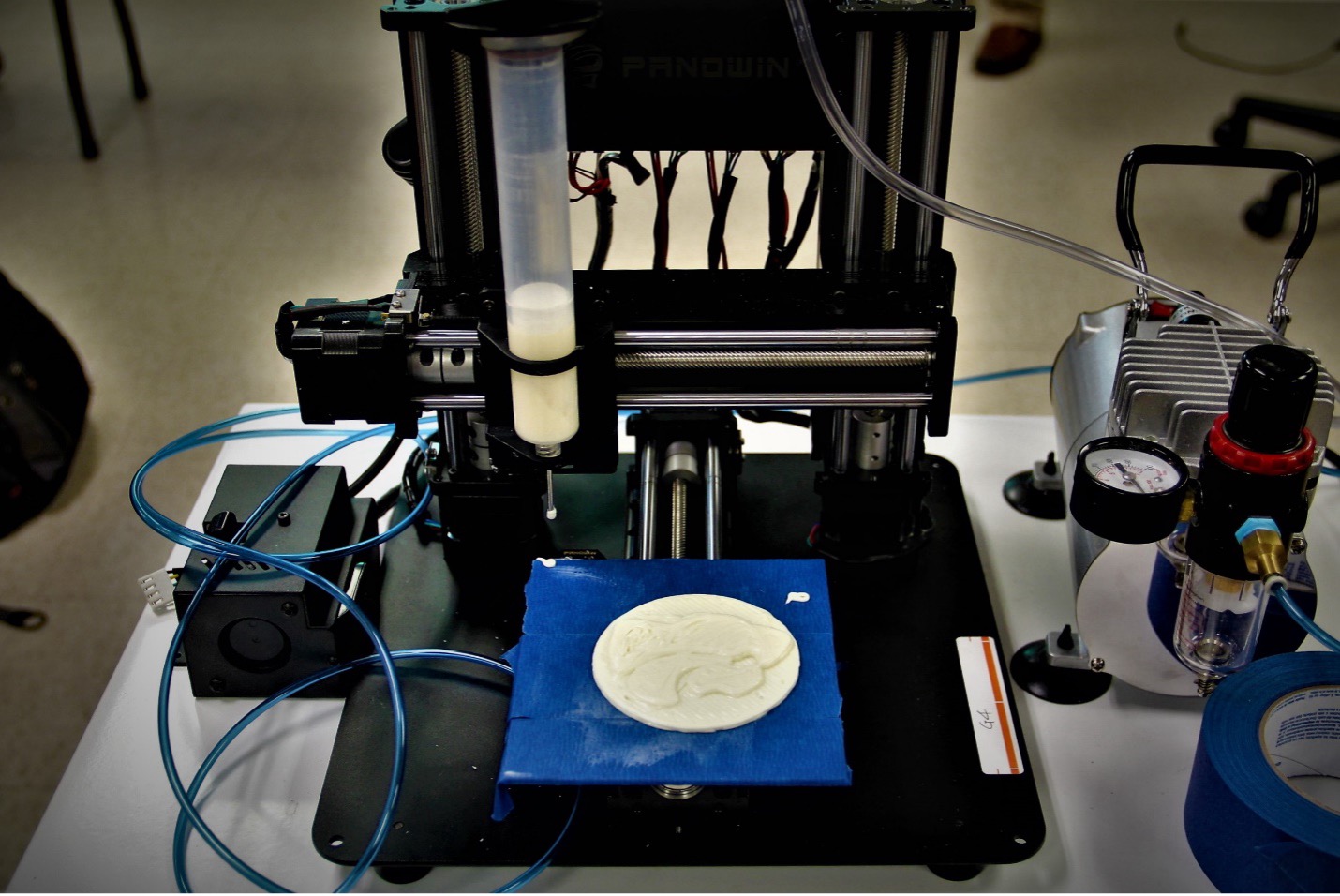
Point-of-care additive manufacturing has the potential to reduce both manufacturing time and overall cost of prosthetics.
Essentially, on-demand 3D printing for medical applications.
“One practical example of this would be custom-fitted prosthetics,” Zhang said. “This process gives you the ability to personalize and individualize in a situation where one-size-fits-all components aren’t ideal, especially in the case of children that grow out of equipment quickly.”
While fitting patients with custom-fitted prosthetic equipment is not a new idea, additive manufacturing of these items on-site can significantly reduce the manufacturing time and overall cost, both of which are better for patients.
Zhang further explained the point-of-care additive manufacturing field by comparing it to personalized orthodontics products that have increased in popularity in recent years.
“The mouthpiece progresses with the treatment plan,” Zhang said. “Those mouthpieces are 3D printed, and every patient has a different requirement and a different plan. Point-of-care additive manufacturing can do those same things with prosthetics in a way that produces better outcomes for the patient.”
Zhang said the process can also be applied to create customized 3D models for medical students that can better simulate the look and feel of an internal organ.
“These medical students can see the structure with high resolution and color, but instead of looking at a computer screen, you’re looking at a model, which better represents everything, even the texture,” he said.
Zhang received more than $300,000 in grant funding from the National Science Foundation’s Division of Undergraduate Education to lead his project, which brings together an interdisciplinary team to help teach the course while working to provide training and mentoring to students interested in this emerging field.
“This training leaves students better suited for working on projects with people from different backgrounds, which is extremely important for engineers.”
“There are two of us with a background in manufacturing, but what makes it unique is that we also have a social scientist, a medical doctor, a bioengineer and a materials scientist,” Zhang said. “You get this expert group doing the training for the engineering students, and those students are being introduced to this field from a diverse set of perspectives.”
The course bridges the fields of engineering and medicine in the manufacturing of a variety of medical devices. It will equip engineering students who are interested in careers in health care, and it provides future medical students with critical engineering skills.
Collaboration is an important element to the project and the course is being taught at another institution simultaneously, with team members facilitating the class through the lenses of their individual disciplines.
“This is admittedly a niche area right now, even though it has shown potential for sizable growth,” Zhang said. “But at the minimum, this training leaves students better suited for working on projects with people from different backgrounds, which is extremely important for engineers.”
Suprem Das, right, is part of a team of K-State researchers developing sensors using atomically thin carbon sheets. From left: Garrett Peterson, electrical engineering; Jaebeom Suh, marketing; Ganga Hettiarachchi, agronomy; Bala Natarajan, electrical and computer engineering; Raj Khosla, agronomy; and Jeongdae Im, civil engineering.
Building soil sensors from nanoscale materials
In the world of enabling technologies, smaller is usually better.
Suprem Das, associate professor of industrial and manufacturing systems engineering, takes this approach with most of his work, including a $2 million grant from the National Science Foundation’s Global Centers program to bring soil sensors for precision agriculture previously operating at the microscale down to the nanoscale.
The project, which includes six other K-State researchers from various disciplines, aims to develop sensors utilizing atomically thin carbon sheets that can more accurately detect nutrients, chemical compounds, soil microbiomes and greenhouse gases in soil in real time. These sensors will give farmers valuable information that could directly impact yield and save the cost of unnecessary inputs.
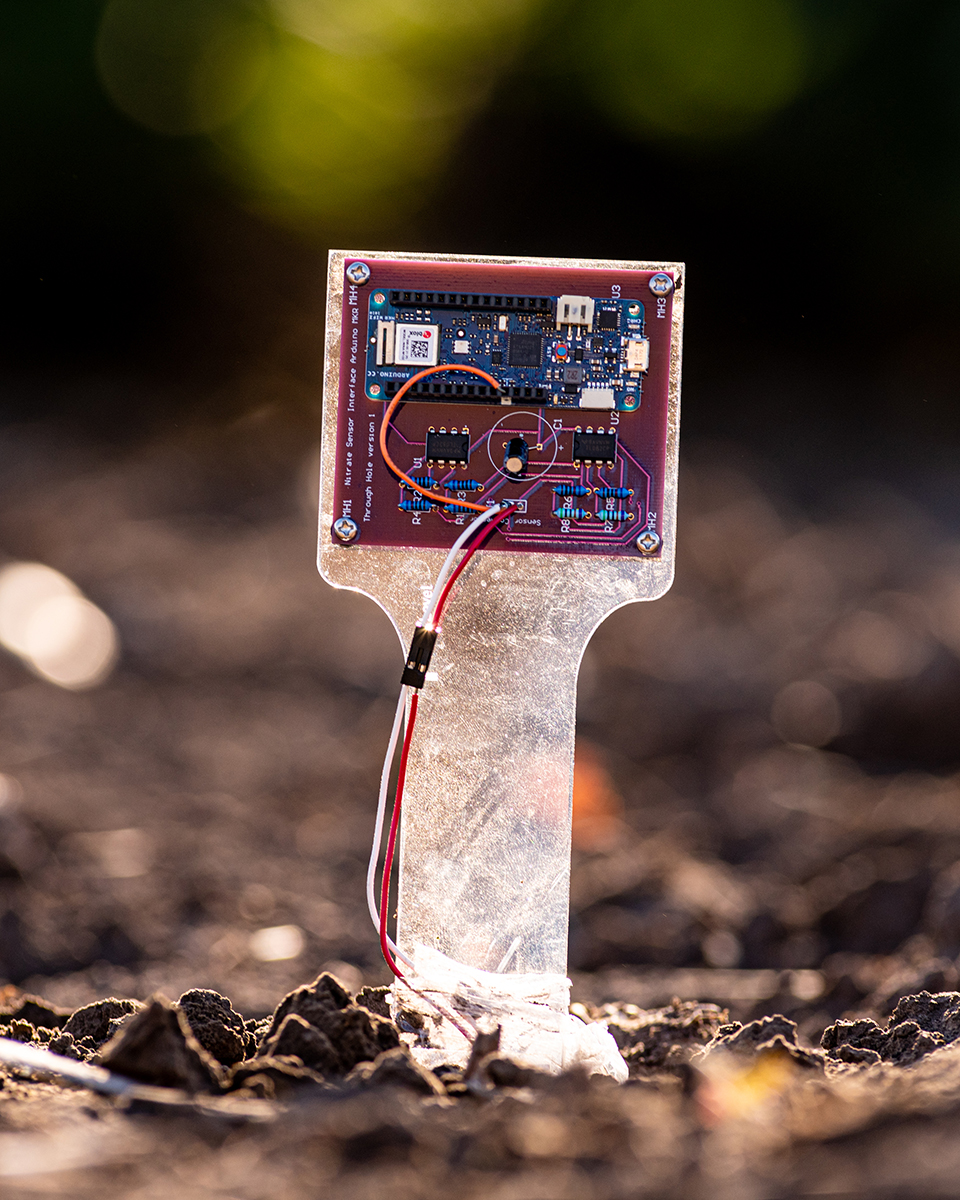
Suprem Das’ team is developing soil sensors similar to the one pictured above, but with the ability to measure at the nanoscale.
But aid in decision-making on the farm is more than just measuring moisture levels and knowing how much fertilizer is in the soil.
Utilizing the large amounts of data generated by these sensors would also allow for further research on other agricultural and environmental issues relating to nitrogen and other problematic gases.
“The overarching goal of this project is the development of this new type of sensor, but also, addressing some of these grand challenges in agriculture,” Das said.
The project builds on previous research by members of the team, including Das’ international Signals in the Soil project that used nanomaterial-based phosphate sensors, and agronomy department head Raj Khosla’s work on biodegradable soil sensors.
“The sensor devices will be small, around a millimeter by a millimeter in size,” Das said. “But if you look at them under a high-resolution microscope, all of them will have materials that are truly measuring at the nanoscale.”
In addition to its practical use in the field, Das sees even broader applications for this technology once it’s fully developed, including repurposing waste products and increasing sustainability.
“Agricultural waste has many contaminants, so it would be really good to collect those waste products — the byproducts — from agriculture, and recover those nitrates,” he said. “We have members of the team who are experts with this recovery process and can help us create this circular bioeconomy.”
“With this highly interdisciplinary team effort, we’re developing these sensors from concepts in the lab to practical application on the farm — all while training the next generation of scientists and engineers.”
Another potential application is the exploration of biological nitrification inhibition, or BNI, chemicals, which occur naturally in some plants and inhibit some of the most volatile and common greenhouse gases associated with agriculture.
“Three of our members are interested in monitoring those BNI chemicals from certain plants, and hopefully, that understanding will give us ways to design new types of BNI,” Das said. “But in order to do that, we need these new biosensors.”
The initial research and testing of the nanoscale sensors is taking place on K-State’s North Farm in Manhattan, but ultimately, the goal is to spread that work to sites elsehwhere in the U.S., Canada and the United Kingdom.
Das is forming a global center to help train students in interdisciplinary research and education and increase understanding of the capability of the proposed sensors.
“With this highly interdisciplinary team effort, we’re developing these sensors from concepts in the lab to practical application on the farm — all while training the next generation of scientists and engineers," he said.
The Technology Development Institute, housed at Kansas State University in the Carl R. Ice College of Engineering, works with clients large and small to solve problems and is celebrating its 40th anniversary in 2025.
Economic development for every corner of Kansas
What began as a faculty-led project to connect K-State researchers conducting manufacturing-focused projects with relevant industry partners in 1985 quickly found a new mission: working directly with clients large and small to solve problems.
K-State’s Technology Development Institute, or TDI, housed in the Carl R. Ice College of Engineering, is celebrating its 40th anniversary in 2025.
The impact on job creation and the Kansas economy are hard to quantify, but since moving into their dedicated off-campus facility in 1995, TDI has completed more than 3,000 projects for more than 700 clients, providing internship opportunities for more than 700 K-State students.
“This work is about working with small companies across the state and beyond and helping people who have ideas,” said Jeff Tucker, executive director of TDI. “We don’t need to write papers; we don’t have to publish. We just do the work, and we educate students along the way.”
TDI is housed in a 22,000-square-foot facility that is packed with machines and equipment. The space is comprised of offices, engineering design labs, a 3D printing and scanning studio and a prototyping workshop.
On campus, faculty and staff at TDI work with university partners to help researchers with prototyping or fabrication, but the bulk of the institute’s clients come from across the state and country. These clients receive resources to help in any number of ways, from engineering and design services to prototyping products to help with patents and commercialization.
“We work with excellent patent attorneys who have clients nationwide,” said Bret Lanz, commercialization director for TDI. “When they’re filing their patents, their next question is ‘Where can I go to get this prototyped?’ So, they pick up the phone and call us.”
While TDI works with external clients on a contract basis, it has also utilized grant support from the U.S. Economic Development Administration and the university to leverage matching funds and help Kansas’ small businesses solve technical problems.
In addition to helping clients, the institute’s robust intern program gives students practical experience, which prepares the next generation of professionals for the industry as they graduate from K-State and begin their careers.
“There’s a workforce development component to what we do, in addition to being a university expertise technical resource,” Lanz said. “We all have a shared desire to help our fellow Kansans thrive and succeed.”
While building physical products is a key part of TDI’s work, Lanz attributes some of its success to a strong reputation from decades of service. TDI serves as an outsourced engineering and design department for small companies that don’t need that type of work on a full-time basis.
“This work is about working with small companies across the state and beyond and helping people who have ideas.”— JEFF TUCKER
For those companies, it’s easier to outsource the work and know it will be handled by the professionals at TDI.
TDI’s work with Helio Next Companies — a private, Kansas-based holding company that focuses on acquiring and operating scalable businesses is one example of that collaboration in action.
Helio Next Companies has brought approximately 50 jobs to the state as it relocates these small businesses to the area.
“We’ve been engaged with at least four of their companies, providing engineering support, developing drawing packages and doing technical design work,” Lanz said.
Jeff Tucker, TDI director, said he is often asked to quantify TDI’s overall impact on the Kansas economy, but it’s an impossible question to answer due to the early stage nature of its work.
TDI’s work enables individuals and businesses to thrive, but the credit for success is shared.
“What we’re doing is throwing out seeds all over the place and waiting for them to sprout,” Tucker said, “which may or may not be the result of our efforts. It comes back to the entrepreneur or the innovator to take it the rest of the way.
“But you have to have the spark to get it going.”
◊◊◊