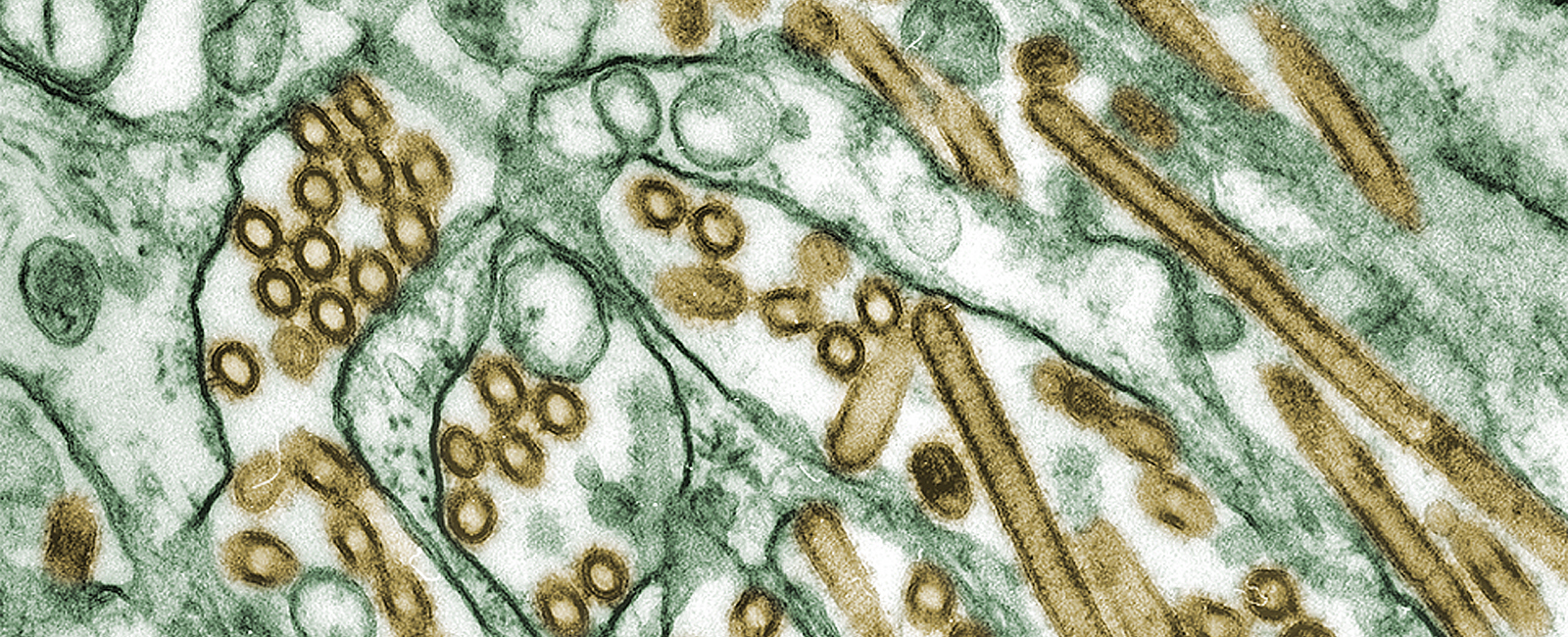
Seek magazine
Seek is Kansas State University’s flagship research magazine and invites readers to “See” “K”-State’s research, scholarly and creative activities, and discoveries.
Reflections and perception
Undergraduate dance research studies self-image and well-being
A master mycologist
Ari Jumpponen, distinguished professor of biology, is a world-leading expert in fungal ecology, but his greatest achievements have been the student minds he's helped cultivate.
<
Cracking the code
Researchers make leaps in identifying, relieving livestock pain
<